The Main Principles Of Roar Solutions
The Main Principles Of Roar Solutions
Blog Article
The 2-Minute Rule for Roar Solutions
Table of ContentsRoar Solutions Can Be Fun For AnyoneThe Single Strategy To Use For Roar SolutionsEverything about Roar Solutions
In order to protect installations from a possible explosion a method of evaluating and classifying a possibly dangerous area is called for. The purpose of this is to ensure the proper choice and installation of devices to ultimately protect against an explosion and to make certain security of life.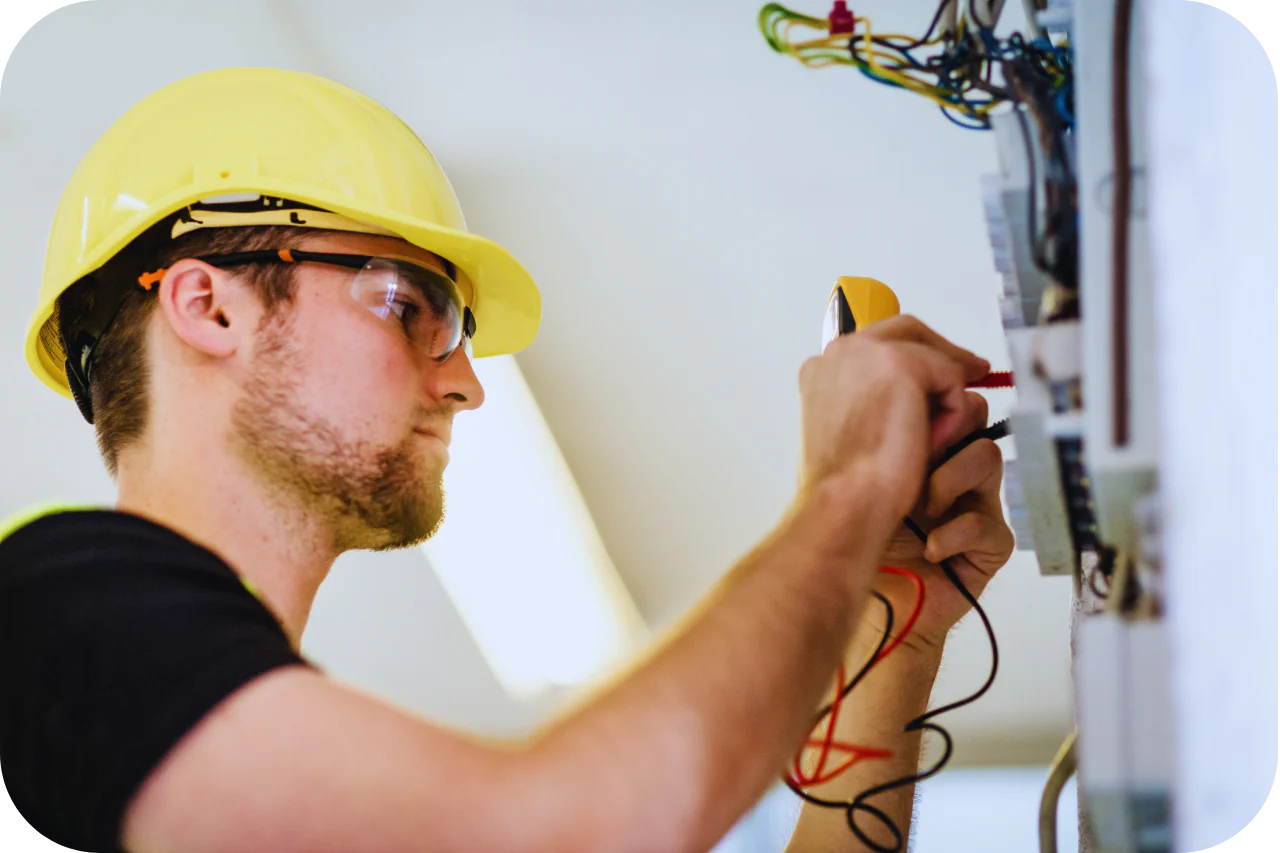
(https://writeablog.net/roarsolutions/html-lang-en)
No equipment ought to be mounted where the surface temperature level of the devices is better than the ignition temperature of the offered danger. Below are some common dust harmful and their minimal ignition temperature level. Coal Dirt 380C 225C Polythene 420C (melts) Methyl Cellulose 420C 320C Starch 460C 435C Flour 490C 340C Sugar 490C 460C Grain Dust 510C 300C Phenolic Resin 530C > 450C Aluminium 590C > 450C PVC 700C > 450C Soot 810C 570C The probability of the danger being existing in a focus high sufficient to trigger an ignition will certainly vary from location to location.
In order to classify this threat an installation is divided right into areas of danger depending upon the quantity of time the dangerous is existing. These areas are referred to as Areas. For gases and vapours and dusts and fibers there are three zones. Zone 0 Area 20 A hazardous environment is highly likely to be existing and may exist for lengthy durations of time (> 1000 hours annually) or perhaps constantly Zone 1 Area 21 A dangerous environment is possible but unlikely to be present for extended periods of time (> 10 450 C [842 F] A category of T6 indicates the minimal ignition temperature is > 85 C [185 F] Dangerous area electrical devices possibly developed for usage in greater ambient temperatures. This would suggested on the rating plate e.g. EExe II C T3 Ta + 60C( This suggests at 60C ambient T3 will certainly not be surpassed) T1 T1, T2, T3, T4, T5, T6 T2 T2, T3, T4, T5, T6 T3 T3, T4, T5, T6 T4 T4, T5, T6 T5 T5, T6 T6 T6 A T Course ranking of T1 implies the optimum surface area temperature level created by the instrument at 40 C is 450 C. Presuming the linked T Class and Temperature score for the tools are ideal for the location, you can always use a tool with a much more rigid Department score than needed for the location. There isn't a clear solution to this question however. It actually does depend on the type of equipment and what fixings require to be accomplished. Equipment with certain examination procedures that can't be carried out in the field in order to achieve/maintain third party rating. Should come back to the factory if it is prior to the devices's service. Field Repair By Authorised Worker: Difficult screening might not be required nevertheless details treatments might need to be followed in order for the equipment to preserve its 3rd party rating. Authorised workers must be utilized to carry out the work properly Repair service need to be a like for like replacement. New part need to be taken into consideration as a direct replacement calling for no unique testing of the equipment after the repair is total. Each piece of equipment with a hazardous rating need to be reviewed individually. These are laid out at a high level listed below, yet for more comprehensive details, please refer straight to the standards.
The 9-Second Trick For Roar Solutions
The equipment register is an extensive database of tools documents that includes a minimum set of fields to identify each thing's place, technical parameters, Ex lover classification, age, and environmental information. This information is vital for monitoring and managing the equipment properly within hazardous areas. On the other hand, for periodic or RBI tasting assessments, the quality will be a mix of Detailed and Close evaluations. The ratio of Detailed to Shut inspections will be figured out by the Tools Threat, which is analyzed based upon ignition risk (the probability of a resource of ignition versus the likelihood of a combustible atmosphere )and the unsafe location classification
( Area 0, 1, or 2). This variation will certainly also affect the resourcing requirements for work prep work. When Whole lots are defined, you can establish tasting strategies based upon the example size of each Whole lot, which describes the number of arbitrary equipment products to be examined. To establish the required sample size, 2 facets need to be examined: the size of the Whole lot and the category of evaluation, which indicates the degree of initiative that ought to be applied( lowered, typical, or boosted )to the inspection of the Whole lot. By incorporating the category of assessment with the Lot size, you can then establish the appropriate denial requirements for a sample, indicating the permitted number of faulty products located within that sample. For even more information on this process, please refer to the Energy Institute Guidelines. The IEC 60079 conventional recommends that the maximum interval in between inspections need to not go beyond 3 years. EEHA assessments will certainly likewise be performed outside of RBI campaigns as part of set up maintenance and tools overhauls or repair work. These inspections can be attributed towards the RBI example dimensions within the influenced Lots. EEHA evaluations are carried out to identify faults in electrical equipment. A heavy racking up system is crucial, as a solitary piece of equipment might have numerous faults, each with differing degrees of ignition threat. If the mixed score of both evaluations is less than two times the fault rating, the Great deal is deemed appropriate. If the Lot is still taken into consideration undesirable, it has to go through a complete inspection or validation, which might cause more stringent inspection procedures. Accepted Whole lot: The sources of any type of mistakes are identified. If a common failing mode is discovered, added equipment may call for maintenance. Mistakes are classified by intensity( Safety, Stability, House cleaning ), making certain that immediate problems are evaluated and resolved without delay to alleviate any type of effect on security or operations. The EEHA data source must track and tape the lifecycle of mistakes together with the rehabilitative actions taken. Carrying out a durable Risk-Based Inspection( RBI )approach is vital for guaranteeing conformity and safety and security in managing Electric Tools in Hazardous Areas( EEHA) (eeha). Automated Fault Rating and Lifecycle Management: Easily manage mistakes and track their lifecycle to boost evaluation accuracy. The introduction of this support for risk-based examination better strengthens Inspectivity's setting as a best-in-class solution for governing conformity, as well as for any type of asset-centric assessment usage instance. If you have an interest in discovering more, we invite you to request a presentation and find exactly how our option can transform your EEHA monitoring procedures.
Examine This Report on Roar Solutions
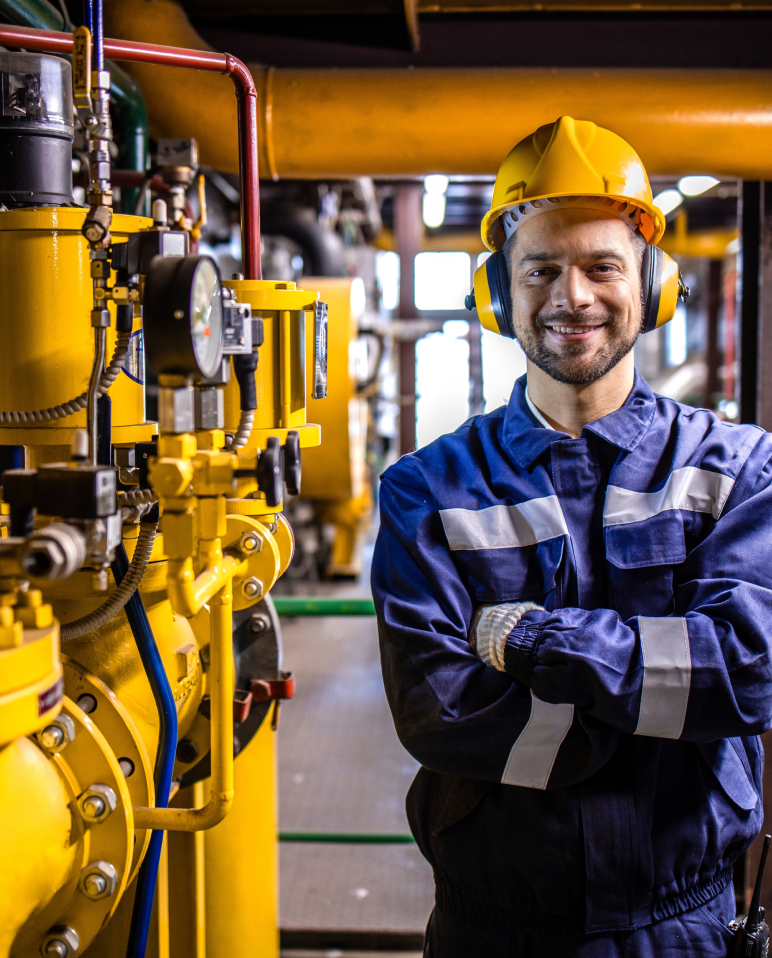
In regards to eruptive danger, a hazardous location is an atmosphere in which an explosive environment exists (or might be anticipated to be present) in quantities that call for special precautions for the building, installment and use of equipment. eeha training. In this short article we explore the obstacles dealt with in the work environment, the danger control procedures, and the required competencies to function securely
It issues of modern life that we produce, store or manage a range of gases or liquids that are regarded flammable, and a variety of dusts that are considered combustible. These substances can, in particular problems, form explosive environments and these can have major and heartbreaking repercussions. A lot of us are familiar with the fire triangle get rid of any kind of one of the 3 components and the fire can not occur, but what does this mean in the context of unsafe areas? When breaking this down into its simplest terms it helpful hints is essentially: a mix of a certain quantity of launch or leak of a particular material or product, blending with ambient oxygen, and the visibility of a resource of ignition.
In most circumstances, we can do little concerning the levels of oxygen airborne, however we can have considerable influence on sources of ignition, as an example electrical devices. Unsafe locations are recorded on the hazardous location category illustration and are identified on-site by the triangular "EX LOVER" sign. Here, amongst other crucial info, zones are split right into 3 types depending on the threat, the chance and duration that an eruptive atmosphere will exist; Area 0 or 20 is considered the most harmful and Zone 2 or 22 is considered the least.
Report this page